现代电炉的液压控制
2.l 共性
现代电炉的技术发展也有共性,最为明显的是:电炉液压控制系统正在朝高压、大流量,高度集成化,以及强化配套件的辅助功能等方面发展。
(l) 泵源的优化
现代大型超高功率电炉液压系统大都使用了高压大流量泵为主工作泵,系统最高工作压力已提高至18
MPa,并使用难燃型的水-乙二醇或合成有机酯为工作介质。系统工作压力的提高,更能适应大型电炉设备结构上的需要,可有效减小液压缸的直径,体现液压控制的传动特点;而大流量液压泵的采用,又减少了工作泵的数量,故可使液压站房的面积大为减小,这样更有利于电炉炼钢区的工艺布置。
(2) 蓄能装置的改进
电炉液压系统须备有处理事故的应急措施,设置液压蓄能装置便是一种常用方法。这是电炉炼钢工艺对液压系统提出的安全技术要求,目的是在紧急情况下,能释放压力油,确保电炉某些重要机构液压动作的完成(如:电极的快速提升,炉体的安全复位等)。由于液体机动容积需求量大,以往的蓄能装置多采用蓄能罐,而蓄能罐的结构特点是气体和液体直接接触,实际使用中,如操作不当,罐中的高压气体就会渗入到管道中产生气泡,严重影响系统正常运行。故现在的系统大都改用了活塞式蓄能器。
相比之下,活塞式蓄能器有很多优点。它既有较大的蓄能量,又能借助自身结构上的特点隔绝气体与液体的接触,同时又可对罐内气体进行加压,完成自身的高压充气。
表l显示:仅有1座电炉液压系统使用的是蓄能罐,其他3座的系统都已使用活塞式蓄能器。显然,后者配置较好。
(3) 紧凑的阀控装置
液压阀优先选用了成套供应的叠加阀,即使有非标加工的液压集成块,各液压阀也都是紧紧围绕集成块的几何面展开布置,实现阀块的高度集成化,详见图l。
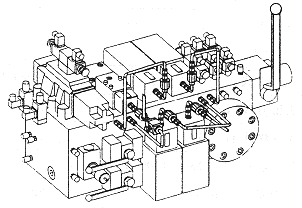
图1 150 t电炉倾动控制液压集成块
(4) 强化配套件的辅助功能
具体包括:
a) 增加减震装置,降低高压泵组的噪声。现在的电炉液压系统,其每台液压泵的传动功率往往为75 kW或90
kW,为降低传动机械噪声,整套液压泵装置都与外部实行柔性连接,即:液压泵的吸油管通过橡胶接管与油箱连接,液压泵的出油管采用高压软管与阀块连接,而传动底座下方设置的弹性减震垫便可使整套液压泵装置整体安放于基础上;
b)
管路增设测压放气点,便于系统调试及日常维护。在电炉机械中,绝大部分液压缸的定位标高都明显高于液压阀台,所以在管路的最高部位增设测压放气点更有利于各油管的放气;
c)
设置过滤器,确保洁净冷却水进入冷却器。这主要是针对冬季冷却器可能不参与工作而设置的,以确保冷却水管在闲置一段时间后能向冷却器输进洁净冷却水;
d) 设置压力表、温度表显示冷却水的实际工况。为了更直观地了解冷却水是否符合要求,以及冷却效果如何,在冷却水管上设置以上两表是有必要的。
2.2 重要控制
(l) 强调与主体设备的配合,提高系统安全性
现代电炉炼钢的重要标志,是工艺自动化控制程度的显著提高,各控制子系统的安全运行和相互联锁是电炉炼钢正常生产的重要保证。所以,现代电炉液压系统除注重自身的可靠性外,更强调与主体设备的安全配合。
最为明显的是,安装在液压缸上的液压阀控装置多了。电炉本体上有一些非常重要的液压控制机构,如:电极升降,炉体倾动,EBT出钢口启闭等机构的液压缸就需要机-液一体化专门设计。由于这些液压缸的缸体在运动,管路连接液压缸时使用了软管,所以要额外考虑软管使用的安全问题,为了确保上述机构能在意外情况(如软管突然爆裂或液压系统失压)下能立即定位而不坠落,一些专用的液压装置就需要从原有的阀台中分离出来而直接安装在液压缸上。这就需要系统设计和设备设计结合起来,共同解决安装问题。这是液压系统与主体设备配合的典型例子,液压系统已不再孤立地进行自身设计。
图2是安装在炉体倾动液压缸上的液压阀控装置。
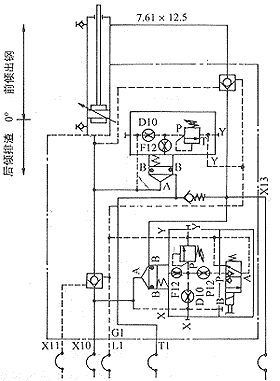
图2 炉体倾动液压缸上的阀控装置
(2) 液压比例控制技术的应用
随着液压技术的发展及大型电炉设备自身的需要,现代电炉的其他一些重要机构,如:电炉炉体倾动,炉盖旋转,炉盖升降等也都同电极升降控制一样采用了液压比例控制。液压比例控制技术的应用较好地实现了机构运行速度的软切换,克服了巨大机械惯性对传动机构产生的不良影响,使机构运行能更加平稳。
例如电炉炉体的倾动。采用EBT(即偏心炉底出钢)技术,是现代电炉炼钢工艺的一项重要标志。在EBT技术中,电炉炉体的倾动角度、倾动速度、回倾速度都变得相当重要,对炉体来说,出钢或排渣过程中,由于倾动角度的不断变化以及自身在某一角度锁定后的再次起动,对其液压传动提出了速度控制要求。图3是国内某钢厂引进的大型偏心炉底式超高功率直流电弧炉的炉体倾动示意图,液压控制使用了比例方向控制阀。
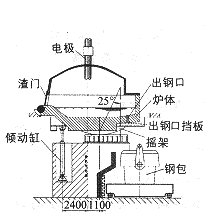
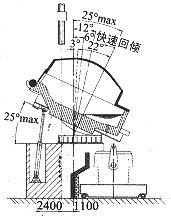
a)冶练 b)出钢
图3 偏心炉底式直流电弧炉的炉体倾动示意图
EBT出钢过程具体如下:
a)首先,炉体以62 mm/s(1°/s)的速度倾至6°并锁定。在确认出钢条件满足后,出钢口挡板便打开,实现电炉首次出钢。
b)在随后出钢过程中,炉体仍以62 mm/s(1°/s)的速度向前倾动(最大倾角为
25°)。当倾至12°时炉体锁定,完成出钢过程中的一次确认;尔后继续倾炉,当钢包中盛装钢水达到标定吨位后,钢包称量装置便发信,指令炉体以186
mm/s(即3°/s)的速度快速回倾,至+3°位置实现减速,并在0°完全停下来。显然,如果炉体的回倾速度太慢,就有可能造成带渣出钢,影响钢水质量,并加重二次冶炼的负担。
由于倾炉采用了液压比例控制,所以炉体每次动作都可实现“慢速起动-匀速运行-慢速止动”的功能,确保运行速度平稳切换。比例控制用于护体这样的超大件运行设备是非常合适的,实际操作效果亦是这样。
2.3 特色控制
(1) 高压蓄能器的充气技术
现代电炉液压系统因使用了活塞式蓄能器,所以在向其充氮气时可利用它的结构特点,借助特殊阀控装置,便能完成充气工作,充气压力最高可达21
MPa,现结合图4说明其具体充气原理。
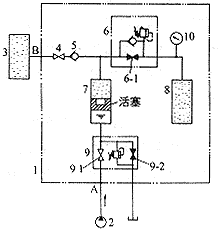
1.蓄能器单元 2.工作泵 3.氮气源 4.截止阀 5.单向阀 6、9.安全阀 7.活塞式蓄能器
8.气瓶 10.压力表
图4 活塞式蓄能器充气原理
a) 首先,蓄能器单元1的A、B两个接口应分别与主系统的工作泵2、氮气源3相连接;
b) 打开截止阀4及阀9-2,并关闭阀9-1。这样,来自气源3中的低压氮气经单向阀5、安全阀6分别进入活塞式蓄能器7的上部和气瓶8中,完成第1次充气;
c) 起动工作泵2,开启阀9-1,关闭阀9-2。此时,来自泵源的压力油经安全阀9进入活塞式蓄能器7的下部,由于安全阀9的压力值设定较高,故压力油足以将蓄能器7的活塞升至顶部,把上部氮气压缩并送至气瓶8中,完成第2次充气;
d) 将工作泵2卸载,关闭阀9-1,打开阀9-2。于是,蓄能器7下部的压力油排入油箱,而其活塞靠上部剩余气压的作用和自身重量开始回落,与此同时,其上部逐渐增大的容腔因负压可再次经单向阀5从气源3中吸入氮气。由于安全阀6中的截止阀6-1是关闭的,故上一次的压缩氮气不会从气瓶8中反向回流;
e) 重复进行步骤c)和d),直至达到系统所要求的充气压力值,该值由压力表10显示;
f) 待充气工作完成后,打开阀6-1、阀9-1,并关闭阀9-2,活塞式蓄能器装置即可投入系统运行。
(2) 电极夹持控制的增压回路
为安全起见,电极夹持液压缸通常采用单作用形式,即电极靠弹簧力支持,由液压力释放。现代大型超高功率电炉的电极尺寸和质量都较以往增加了许多,为了增大夹持力,设计人员往往力求改进弹簧性能,增大弹簧力,这样可减少夹持器与电极的接触面积,提高电极导电性能;而为了克服较大弹簧力,减小液压缸直径,在不提高系统压力的情况下,一些设备供货商在系统控制上进行了技术改进,即使用增压器。增压器的形式有多种,但其实质上是一个微型双作用液压缸,只要将其串联在回路中,利用两腔几何面积比,即能达到增压目的。经增压器排出的高压油进入电极夹持液压缸,足以克服弹簧力作用,打开夹持器将电极释放。德国DEMAG公司和奥地利FUCHS公司提供的电炉设备中就常使用这种机构,分别见图5和图6。
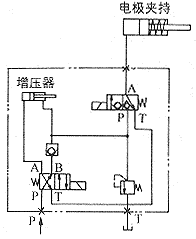
图5 DEMAG公司的增压回路

图6 FUCHS公司的增压回路
(3) GHH型直流电弧炉底电极更换液压装置
直流电弧炉因底电极不同而各具特色。德国GHH公司提供的直流电弧炉,其底电极为风冷式棒针型,属三大型之一,俗称GHH型。其特点是投资少,但维修量大。值得介绍的是它的底电极更换机构,见图7,这是一个特殊的液压同步顶升系统。机构中共设置6个液压缸(其中3个为伸缩式),顶升动作共分3个步骤完成:先是6个液压缸同时行程200
mm,将底电极预松动一下;接着,3个伸缩式液压缸再行程1800
mm,将底电极顶出;最后,由行车调走底电极。整个顶升过程对6个液压缸有较高同步性要求。图7是其液压控制原理,回路中共使用了2个同步机构(同步液压缸和同步液压马达)来保证液压缸的运行同步性。具体工作程序如下: